Working in the marine and offshore industries or supplying products for marine applications often requires ABS certification. Understanding where in the manufacturing or construction process the certification is required and working with your suppliers can help you minimize costs and production delays while ensuring that your products obtain the certifications needed.
WHAT IS ABS?
The American Bureau of Shipping (ABS) was chartered in 1862 to certify ship captains. Since then, it has been involved in developing and setting safety and quality standards for ships and offshore structures. ABS standards are recognized globally and are used to ensure that the materials, parts and components, and construction of vessels and marine equipment meet established safety standards. ABS works with the marine industry worldwide as they develop new technologies for constructing marine vessels and offshore structures, revising and updating its certifications to meet the changing industry needs.
The Rules and Grades established by ABS for certification are written to provide standards for the design, construction, and periodic survey of marine vessels and offshore structures to promote their safe design and assembly. Materials, parts, and components used in the manufacture of marine vessels and structures must meet the set standards for the vessel or structure in which they will be used.
Certifications are specified by the Rules, such as Steel Vessel Rules part 2-3-7/1, or MODU (mobile offshore drilling unit) Rules, or the material grade, such as Grade 2, or Grade 4C.
The end use of the component determines the inspections and certifications required, as well as any requirements for inspections during manufacturing:
- Certain components used in the construction of the vessel or structure must be certified
- Some of those components must be certified (inspected) as they are being constructed or fabricated to verify that the construction meets ABS standards
- Some materials must be certified during manufacturing; this will minimize the need for additional certification during construction or fabrication
Information about ABS certifications can be found at www.eagle.org.
MINIMIZING RISKS AND COSTS
ABS certification costs time and money. Certification inspectors are on-site at your facility during manufacturing, construction, or fabrication to verify that your processes meet the standards - and you pay for the time they are on-site. So, it’s important that you understand the Rule requirements for your product to identify the stages in your supply chain where inspection and certification should occur. By doing so, you’ll save your company time and money, and minimize the risk of your products not being certified. Some simple steps can provide you with cost and time savings.
Know what the requirements are for your product.
Answering a few questions will help:
- Which ABS Rules or ABS Grade applies to your product?
- What is the application that your component will be used for? For example, are you manufacturing a component for a jacking system (or the complete system), torque transmitting parts, or a structural component? The application helps determine the section of the Rules or Type Approval Tier that is appropriate for your part.
- What is the end use of the part? The end use of the part is also used to determine which ABS Rule, Grade or Type Approval Tier is required. For example, if your part is a component in a tailshaft, the process required may be different than if it is being used in rudder stock.
- Do you have an ABS-approved drawing or Design Approval Document? These drawings or documents show that ABS has approved the design as well as provide an approval number for reference.
Partner with your suppliers.
It is critical to flow-down your ABS requirements to your suppliers...and your entire supply chain. This is the most important aspect to ensure your component will be accurately certified. It may be required for your suppliers to have inspection performed during the manufacturing process. Clear requirements throughout the supply chain ensure that your component is manufactured under the certification requirements without delays or added costs.
Often, by the time the purchase order is submitted to raw material vendors, the ABS Rule requirements are missing. This is caused because the requirements were not flown-down the supply chain.
- An ideal PO includes information on the all the ABS Rules and Grades or the Design Approval Document from ABS.
- Your supplier should work with you to ensure that the inspections and certifications are handled at the most effective point in the manufacturing process, eliminating time-consuming errors and reducing inspection costs.
- It is helpful to have a supplier that is approved by ABS. Using certified suppliers can further minimize the cost and lead-time of inspections (ex: if you need a forging where final heat treatment will take place at another level within the supply chain, and the forging facility is an ABS- Approved supplier, then inspection may not be required at the forge level).
With some planning, answering a few questions, and partnering with your suppliers, you can improve the efficiency of your production and reduce the costs of certifying your products for use in the marine industry.
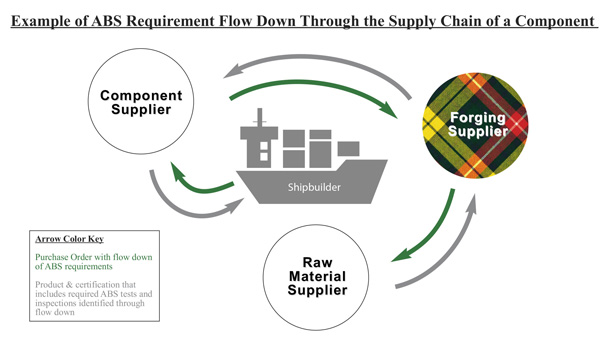
THE SCOT FORGE ADVANTAGE
At Scot Forge, we are uniquely qualified to provide you with ABS-certified products and materials. We are one of the few U.S. companies that have been audited by the American Bureau of Shipping and APPROVED as a worldwide ABS forging supplier. Our technically trained sales staff has extensive experience manufacturing ABS-certified products and will partner with you to ensure that your part has all the requirements to ensure certification while minimizing time and costs. We are a custom manufacturer of open die forgings and seamless rolled rings, with the capability to forge parts up to 100,000 lbs. and roll rings up to 252” in diameter. From gear box repair to broken rudder stock, contact us at today see how we can help you with your marine part and get you out of dry dock and back in commission.
Click here to download the Working with ABS Certifications PDF.