Metalworking and Movable Bridges
- SCOT FORGE
- Dec 8, 2022
- 4 min read
When bridge owners must select a process and supplier to produce a critical metal component, they face an enormous array of possible alternatives. Many metalworking processes are available, each offering a unique set of capabilities, costs and advantages.
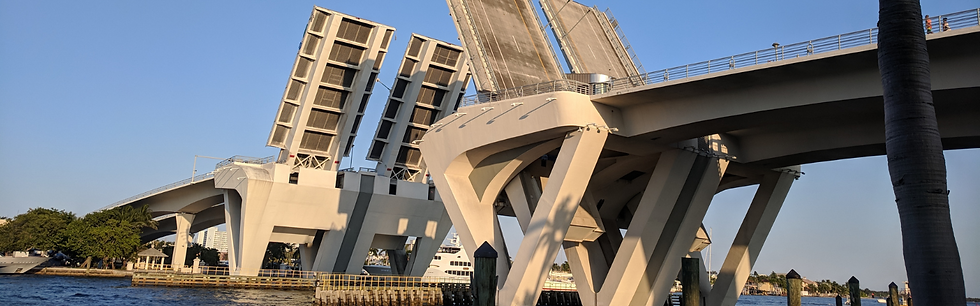
When bridge owners must select a process and supplier to produce a critical metal component, they face an enormous array of possible alternatives. Many metalworking processes are available, each offering a unique set of capabilities, costs and advantages. The forging process is ideally suited to many part applications. In fact, forging is often the optimum process for both part quality and cost, especially for applications that require maximum part strength, custom sizes or critical performance specifications. So why did so many engineers choose castings over forgings at the peak of bridge construction (c. 1960)?
Unfortunately, most federal bridge safety standards were not created until the late 1960s in response to the Ohio River bridge collapse. The failure was caused by the bridge's corrosion and decay, which weakened it to the point of collapse, killing 46 people. After analysis, it was discovered that a microscopic crack formed in a steel eye bar used in the bridge's construction during the casting process. Over time stress and corrosion fatigue caused the crack to grow until the component failed. Today, it is well known that castings lack the continuous grain flow, refined grain structure and directional strength necessary for critical, load-bearing operations. The lack of properly oriented grain flow and refinement can lead to potential part integrity problems causing failures in the field. In the1960s, hundreds of casting foundries in the U.S. could supply the complex or large metal components required for bridgework. In addition, castings were cheap and plentiful compared to steel forgings at that time. As demand for steel castings outpaced supply, however, companies began to look outside of the U.S. and Canada for solutions, which ultimately impacted the supply chain in two ways:
1) It gave birth to an offshore option for steel castings which reached its height and inflicted significant damage on the domestic industry in the following decades.
2) OEMs were not content back then to wait for the offshore option to develop fully, so casting users moved aggressively to invest in a substitute process – steel fabrication. In fact, the presence of fab shops within virtually every manufacturing plant – which we take for granted today – did not exist before the late 1970s and is the direct result of those mentioned above.
The North American steel foundry industry is a shadow of its former self. In 2015, fewer than 200 steel casting plants remained, down from a 1970s high of more than five times that many. Today's more demanding material users are increasingly obliged by everyday economic and competitive realities to seek a better supply-chain solution and stronger, sounder and technically superior product. However, when deciding on bridge construction and repair, the question still is … "casting, fabrication or forging?"
BEARING HOUSINGS
Manufacturing components with a welded plate or welded ends produce quality issues from inconsistencies in using different metalworking processes. Inclusions are common, and welded parts often require extensive weld repair and re-inspection. By making the component a single forged piece with integral flanges, quality is improved throughout the part, eliminating instances of inclusion and removing the welding time altogether. The strength and structural integrity of the forged material meets demanding application requirements, resulting in less rework, fewer rejections and increased part life. Additionally, eliminating welding shortens part production process time, and the component is better able to withstand the rigors of field use.
PINIONS, FLOATING SHAFTS, TRUNNIONS
Machining a solid bar to form a pinion, floating shaft, or trunnion causes wasteful use of material, labor and time. Inclusions are common on the machined surface, which may cause product rejections and result in excessive time and costs spent repairing the part. Additionally, grain flow within the bar is exposed when machined, thus making the material more susceptible to fatigue failure due to exposed grain ends. On the other hand, custom forging requires less starting material than a straight round bar machined to shape. Material cleanliness is optimized by controlling melt practices and teaming processes, eliminating material rejections due to inclusions. Less machining saves money, time and tool life while producing a closer-to-finish shape. Lastly, a forged stepdown contoured grain flow yields greater impact and directional strength.
ANCHORAGE BARS AND LINKS/GUDGEON ASSEMBLIES
This product is often made from a cast head welded to a hot rolled bar. Due to the lack of uniform grain structure within castings, this product often proves too weak for the intended application, resulting in shortened product life. Cracking is typical in the weld layer, causing failures in the field. Additionally, welding the two pieces together is time-consuming. The excessive heating required during the welding process changes the hardness and tensile properties in the weld zone, making it necessary to re-heat treat the part. Fortunately, this product can be manufactured as a single-piece forging instead, improving properties and eliminating non-value-added steps. The elimination of welding provides dimensional stability, reduces the amount of inspection and simplifies inventory management. Most importantly, the strength and structural integrity of the forged material meets demanding application requirements, resulting in less rework, fewer rejections and increased part life.
CONSIDERATIONS
If you are looking for a new approach to repairing infrastructure, there are many factors to consider when converting a historic design. Often, securing engineering's approval is the key to making enhancements. When reviewing your component, it is helpful to take a step back and ask, "What is the purpose of my design?" The best results occur if you're willing to think creatively and challenge traditional methods.
If you are considering forgings, you should partner with a supplier willing to work with your engineers to educate them about conversions, forgings and the newly expanded range of product types (complex parts) that can be produced as a forging. Rather than dismissing the idea as impractical or impossible, consider the technical and/or economic merits of any particular conversion project.
Comments